The ten most common defects in glass bottle forming.
(1) Crack. Cracks are the most common shortcoming of glass bottles. It can be very thin, and some can only be found in reflected light. Frequently produced parts are the mouth, neck and shoulders, and cracks often occur on the bottle and the bottom of the bottle.
(2) Uneven thickness. This means that the glass on the glass bottle is unevenly distributed. The main reason is that the temperature of the glass gob is not uniform, the part with high temperature has small viscosity, and it is easy to blow thin; the part with low temperature has large resistance and thick. The temperature of the model is not uniform, and the glass with a high temperature is cooled slowly, and it is easy to blow thin, and the side with a low temperature is blown thick due to the rapid cooling of the glass.
(3) Deformation. If the gob temperature and the applied temperature are too high, the bottle which is released from the forming die is not completely shaped, and tends to collapse. Sometimes the bottom of the bottle is still soft and will print the marks on the conveyor belt to make the bottom of the bottle uneven.
(4) Not full. If the gob temperature is too low or the model is too cold, the mouth, shoulders, etc. will not be full, resulting in defects such as gaps, shoulders and unclear patterns.
(5) Cold spots. A plaque that is not smooth on the surface of the glass is called a cold shift. The main reason for this defect is that the model temperature is too cold, which occurs when starting production or shutting down production.
(6) Prominence. A defect in which the glass bottle is protruding or the edge of the mouth protrudes outward. This is due to the fact that the model parts are not manufactured correctly enough or the installation is not well matched. The model is damaged, the joint surface is dirty, and the top core is too late to enter the position. Before the glass frit has fallen into the initial mold, a part of the glass is pressed out or blown out from the slit.
(7) Wrinkles. Wrinkles come in a variety of shapes, some are creases, and some are very thin wrinkles. The reason for wrinkles is mainly due to the fact that the gob is too cold, the drip is too long, and the gob does not fall in the middle of the initial mold and sticks to the cavity wall.
(8) Surface defects. The surface of the bottle is rough and uneven, mainly due to the matte surface of the cavity. If the model's lubricating oil is not clean or the oiled brush is too dirty, it will also degrade the surface quality of the bottle.
(9) Bubbles. The bubbles generated during the forming process tend to be several large bubbles or a number of small bubbles concentrated in the same, which is different from the evenly distributed small bubbles of the glass itself.
(10) Scissors. The obvious traces left on the bottle due to poor shearing. One branch often has two scissors prints, and the upper scissors are left at the bottom, which affects the appearance. The scissors below are left in the bottle mouth. It is often the source of cracks.
Navigation
Stay in touch
Cable Solution for Telecom
QR code
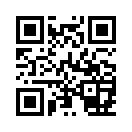